Resources - Blog
Circular Textile Techniques Unravelled
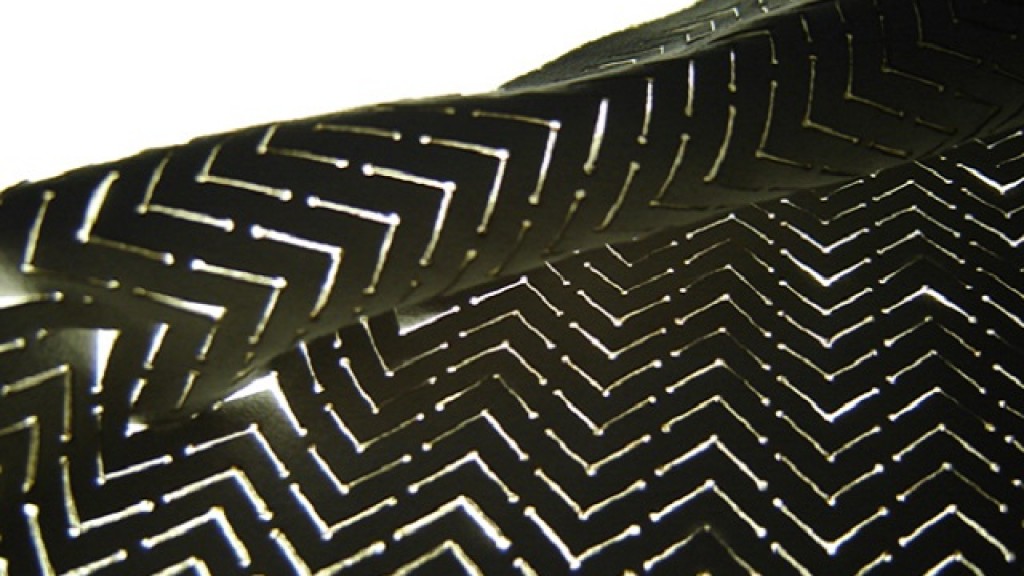
Fioen van Balgooi helps companies that design textile products become more circular by being part of the design team as an ‘eco-effective’ designer, sourcing materials & techniques and doing research & development in this field. Here she talks us through a few techniques that make decorated textiles easier to disassemble.
Designing for disassembly is one way to ensure your products are becoming more circular. As a designer working towards a circular economy, disassembly means your raw materials can then be used for other products. In textile design, often fabrics are decorated with techniques such as silk screen printing. But what happens if you use prints on a textile? You leave behind a material on the fabric that most of the time cannot be removed, biodegraded or recycled.
In this blog article I am going to introduce you to different techniques that can be used to design decorated textiles in a way which makes it possible to disassemble the materials and biodegrade, reuse or recycle them.
Laser cutting and etching
Using a laser you create different effects on a textile. When cutting patterns you can create a design where by different layers are visible through each other. It’s also possible to make stiff fabrics more flexible when you cut different line designs in the textile. If you use laser etching (not cutting all the way through, more like ‘scratching the surface’) you are able to create grey scale prints. The effect works very well with fleece and velvet fabrics. Also interesting results can be made with flexible bio plastic materials.
Laser Cutting
Laser Etching
Memory melting
Synthetic materials have an interesting property: when they are heated they melt and when they cool down they remember their new form. This can be used to decorate synthetic textiles by creating folds in many different ways.
Wear2 ecostitching technology
This is a dissolvable yarn. You can stitch with it like any other yarn on normal industrial machines. When exposed to microwave radiation the yarn loses about 80% of its tensile strength. The textiles stay unharmed, and after the treatment pulling lightly on the seams causes the yarn to break, which then allows components to be easily separated.
Punching
With punching you attach two materials to each other using needles with barbs. Your fibre and textile choice is very important with this technique in order to make it suitable for eco-effective designing. If you use a woolen fibre, also use a woolen textile as a base layer. In this way the woolen textile is still biodegradable (if it is dyed with biodegradable dyes) or recyclable. When using a synthetic fibre punching is possible but it becomes more difficult because these fibres are very smooth.
Punching
Removable prints
Inks are currently developed to be permanently fixed and last as long as possible. But this is not in line with designing for a circular economy. If you want to design for disassembly and reuse it would be better if you were able to remove the ink from the fabric at the end of its life. Refinity has developed removable ink and is currently seeking for partners to improve the ink and make it available on the market.
Removable Ink
3D printing
With 3D printing you can create textile-like materials from biodegradable plastics or recyclable plastics. There are currently flexible materials that can be printed in 3D. For example TPU 92A-1, which is used by Iris van Herpen and developed by Materialise to create a dress.
Liz Havlin is working on an open source project that turns recycled plastic into 3D printer ink. The extruder she is creating is called the Legacy and designed by inventor Hugh Lyman.
Challenges and opportunities
As you can see there are a lot of new possibilities and old techniques in a new form that can be used to design textile products for effective disassembly. But I can imagine there are also some challenges that keep you from doing so. Please tell me in the comments below what you think is needed to make designing for a circular economy a success.
I hope these techniques inspired you and you cannot wait to start implementing eco-effective designing in your company working towards a circular economy! If you would like to know more, go to www.refinity.eu