Resources - Blog
Redesigning the razor – Life Cycle Assessment
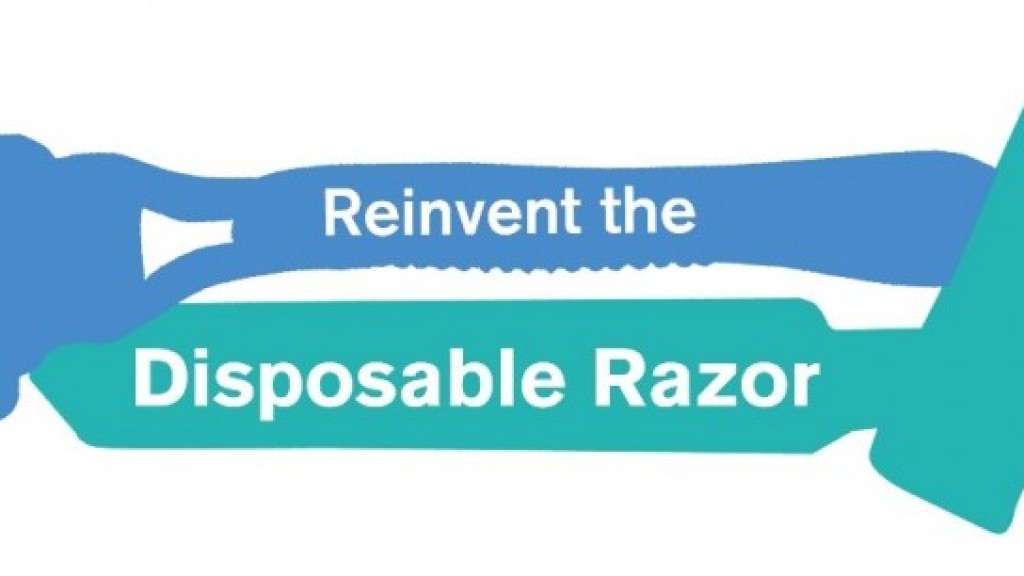
This is the fourth installment in a series of blogs in which we explore how to design a product for circularity. Here, Great Recovery Intern Sebastian de Cabo Portugal discusses Life Cycle Assessments.
When designing a product for circularity it is often difficult to know where to begin. Therefore, to help designers get started and make informed decisions, a Life cycle Analysis (LCA) can be carried out using the information gathered during the research stage.
LCA is a technique to assess the environmental aspects and potential impacts associated with a product, process, or service. This assessment is exceptionally useful as it shows the designer what areas are the most impactful during the product’s life cycle. For example, the designer might think that the manufacturing stage would be the most impactful, when in reality for some products it’s the raw material extraction or its use phase. It can also help them to compare the newly redesigned product to the original, acting as a benchmark to ensure the design changes are actually positive for the environment.
However, the LCA is not an exact science and has its limitations:
•Uncertainties about the correctness of the model. There is always some level of uncertainty in the results and in the methodology; so users shouldn’t take the numbers shown as absolute values, but more as a guide to prioritise work. Not all form of impacts are valued the same, so the ones with the largest impact should be tackled first in order to produce the maximum overall improvement.
•Data Uncertainty. Gathering all the data for the LCA is the most difficult part of the task, and normally assumptions have to be made where it’s impossible to gather all the knowledge required, thus not all the relevant impacts are considered. In this case it’s much harder for me to carry out an LCA on a Gillette razor than if Gillette did the LCA themselves, as they would have all the correct info required first-hand (reducing the number of assumptions needing to be used).
Eco-Indicator Assessment
The Eco-Indicator method is a tool developed to help designers conduct a simplified LCA study. The advantage of using this method compared to a more comprehensive LCA method is that it’s much simpler to carry out and to gather the required information because the data regarding the most common materials and processes has been collected in advance. This makes it an easy and quick method to start the analysis of a product and aid the designer when creating alternative concepts which are more environmentally friendly, because they can clearly identify what areas need improvement and which ones work well already. Another advantage is that the process produces a single score (Eco-Indicator Point) for the all the impacts of the product, not just individual ones for each part. These are the reasons why I will carry out an Eco-Indicator Assessment instead of a full LCA.
In order to carry out the Eco-Indicator analysis method, the methodology described below has to be followed:
1.Establish the purpose of the Eco-Indicator calculations
2.Define the life-cycle
3.Quantify the materials and processes
4.Complete the form
5.Interpret and analyse the results
In this post I haven’t shown the whole process, but there are downloadable links to my full Eco-Indicator results, and to the template form if you’d like to carry out an assessment yourself.
1. The purpose of this assessment is to compare two different types of razors: cartridge based vs. double edge safety razor.
These results will then be used to inform the design process and improve the redesigned razor. Finally, the assessment will be carried out on the new design to assess if it has a lower impact than the other options analysed.
In this section we also need to state the assumptions made during the process:
•The blades and lubricating strip were too light to be measured with our equipment so their weights were rounded to 1g.
•The Eco-Indicator for EPDM rubber includes the manufacturing of the rubber as well as the molding process.
•The tables didn’t contain values for welding steel, so it has been assumed that the value is close to welding aluminium which is in the table.
•It has been assumed that the only part recycled at the end of life is the packaging.
•It has been assumed that the packaging contains cardboard, even though it has been made from other natural fibres like bamboo, as there is no info on those materials in the Eco-Indicator tables.
•The product doesn’t contain any material labels, so the materials have been assumed to be low alloy steel for the body, PP for the plastic parts of the body, EPDM rubber for the grip and an acrylic polymer coating for the lubricating band.
2. Define the Life-cycle – This is an example of a simple product life-cycle diagram. In this case it’s the life-cycle of the cartridge-based razor.
3. Interpretation of results – The last step in the process is to interpret the results and compare them against each other.
The hardest part of this whole process is the data gathering. In this case it was very difficult to see what materials the product contained and exactly how it was manufactured (as the big manufacturing companies wouldn’t disclose this information), so some of the data had to be assumed. This obviously makes the results less accurate, but it can still be used as a general indicator of impact.
The final value for the cartridge-based razor was 115.06 mPt, and the value for the double edge safety razor was 15.70 mPt. The biggest impact during the cartridge-based razor life-cycle is manufacturing the cartridge as this is the part which is hardest to make. In landfilling or incinerating this part, the large amount of energy and material value used in creating it is lost. By far, the biggest impact during the manufacturing of the razors was the 17 spot welds done in each cartridge.
We can see how the double edge safety razor has a much lower impact due to the low amount of parts and materials used and the fact that the blade can be separated from the rest of the body and recycled (reducing the overall impact of the product).
The body of both razors had similar impact as their weights were also quite similar. The cartridge-based razor had a slightly higher impact due to the rubber parts which can’t be separated from the plastic body.
Now that we understand the key challenges with the razors, and where the biggest impacts are occurring, we can begin to make informed decisions in the redesign. My next blog post will show some design recommendations using sketches and 3D-printed prototypes.
This project is a collaboration between the Great Recovery Programme and Fab Lab London.